ThermAlloy® Thermal Spray Process
1. Clean Part & Qualify for Repair
The substrate surface of power cylinder bores are prepared by cleaning and degreasing.
The parts are magnaflux tested. This determines if the part is repairable or not. Internal and outside dimensions are documented, along with content of material and hardness of material.
- Typically, parts are placed in a vat of caustic soda for 24 to 48 hours.
- Cylinder bores are pressure-tested and magnaflux tested.
2. Bore Process & Oven Cycle
All pipe plugs and oil lines are removed from the cylinders. The part will be bored out to .035 on the diameter up. No more than .100 on the diameter. Most cylinders can be rebuilt 4 to 5 times of the life of the cylinder.
If the outside dimensions are out of standard then the outside dimensions will be built back up using an aluminum bronze.
The cylinder or other parts is placed in a 700 degree oven for 12 to 14 hours to ensure all oils have been removed.
3. Coating Application
ThermAlloy® is a revolutionary process for to repair power cylinder bores. Exline, Inc. created this process as an alternative to hard chrome plating through advances in thermal spray coatings, and application equipment technology.
ThermAlloy® (Exline's proprietary thermal spray coating) in the bore of the cylinder, Babbitt coating in the piston, and Safety Seal (piston ring) is the perfect recipe for extending the life of your cylinders and pistons.
Consider ThermAlloy® instead of hard chrome for rebuilding compressor's essential components.
5. Pressure Tested & Checked
The parts are washed and assembled. Pipe plugs and oil lines are pressure tested to ensure quality.
Testing includes pressure test, surface test and hardness test. Parts are double-checked by different people to ensure quality parts are shipped to the customer.
Final cleaning, assembly, pressure testing, painting, packaging and final inspections are completed before shipping to the customer.
Advantages of ThermAlloy® Coatings
ThermAlloy® (Exline's proprietary thermal spray coating) in the bore of the cylinder, Babbitt coating in the piston, and Safety Seal (piston ring) is the perfect recipe for extending the life of your cylinders and pistons.
Consider ThermAlloy®
instead
of
hard chrome for rebuilding compressor's essential components.
Have Questions?
Thermal Spray Process Contact
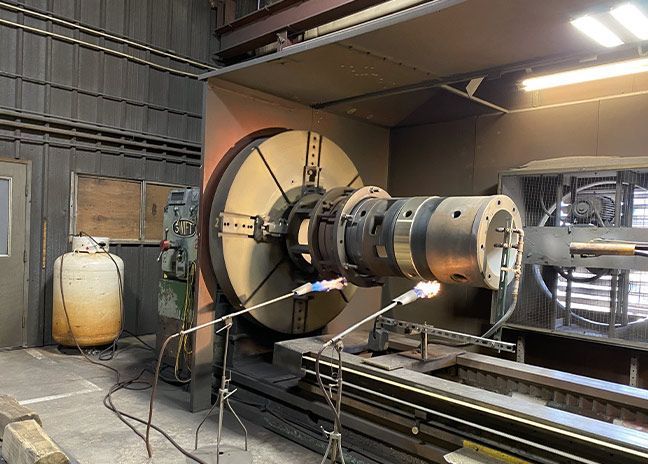