Thermal Spray Coating Process
Exline's thermal spray coating process is also known as ThermEx® Thermal Spray Coating Systems is a surface modification technique used to apply protective or functional coatings to various materials. It involves the application of a melted or heated coating material onto a prepared substrate surface. The coating material is typically in the form of powder, wire, or rod.
Restore parts to "better than new" condition. Compare our ThermEx® Thermal Spray Coatings to Hard Chrome Plating.
ThermEx® Thermal Spray Process
Advantages of Thermal Spray Coating
The thermal spray coating process offers several advantages, such as the ability to apply a wide range of coating materials, excellent bond strength, and the capability to create thick coatings.
It is used in various industries, including:
- aerospace
- automotive
- energy
- oil and gas
- manufacturing
ThermEx® thermal spray coatings provide coatings for purposes such as:
- corrosion protection
- wear resistance
- thermal insulation
- electrical conductivity
- improved surface properties
CONTACT
Thermal Spray Coating Options:
At Exline, Inc., we offer a variety of thermal spray coating options. Extend service life by restoring original dimensions, and adding corrosion protection.
Repair your cylinders, compressor rods, compressor pistons, camshafts, crankshafts, main bearing saddles, plug valves, power cylinders, power cylinder liners, power pistons, turbine components, and roller coatings.
Most frequently used coating options are:
- 400 Stainless Steel
- Tungsten Carbide
(lasts 6 to 10 times the life of hard chrome) - Aluminum Oxide Ceramic
- Zirconium Oxide Ceramic
- Copper
- ThermAlloy®
Consider ThermAlloy® instead of hard chrome for rebuilding compressor's essential components.
List of Services
- 1. Zirconium Oxide Ceramic
- Thermal barrier applications
- Piston crowns and turbo exhaust inlets
- 2. Alumina-Titania Ceramic Composite
- High wear applications
- Compressor rods, pump plungers, sludge pump pistons, grinder spindle bearing areas
- 3. Aluminum Oxide Ceramic
- High dielectric strength
- Mounting devices
- 4. Aluminum Iron
- Antiskid application
- Floor decking, stairsteps
- 5. Aluminum Bronze
- Connecting rod pin eyes and crank eyes, flywheel bores, pump impellers, piston skirt build up material
- 6. Babbitt
- High-grade, lead-free Babbitt
- Bearings, crosshead slippers, piston skirts
- 7. Copper
- Good electrical conductivity, copper reclamation
- Carbon brushes, resistors, capacitors
- 8. Zinc
- Protection for iron and steel against corrosion
- 9. 400 Stainless Steel
- General purpose build up
- Compressor cylinders, hydraulic rams, bearing journals, tapered plug valves, compressor rods
- 10. Proprietary Material
- High wear applications
- Pump plungers, Compressor rods, camshafts journals
- 11. Hard Chrome
- High wear application
- Corrosion protection
- (Outsourced process, Exline prefers other thermal spray process.)
- 12. Tungsten Carbide Cobalt
- High Wear Application
- Compressor rods, pump plungers, air lock rotors, wrist pins, pump impeller sleeves, gate valves
Have Questions?
Thermal Spray Process Contact
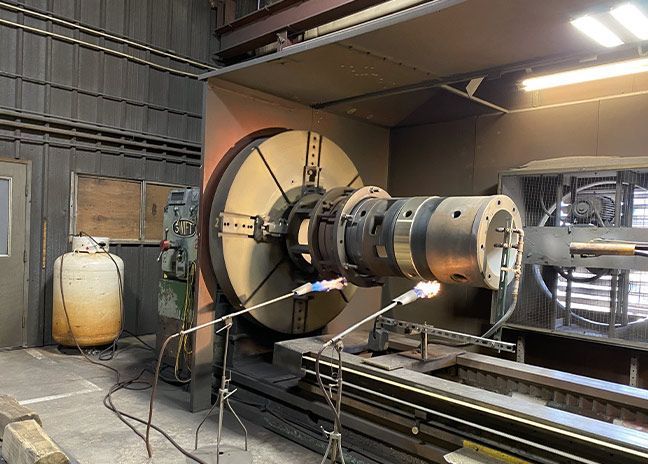